Schalenformgussist ein Prozess, bei dem der mit einem duroplastischen Harz vermischte Sand mit einer erhitzten metallischen Musterplatte in Kontakt kommt, so dass sich eine dünne und starke Formschale um das Muster herum bildet. Anschließend wird die Schale vom Modell entfernt, Oberkasten und Unterkasten gemeinsam entfernt und in einem Behälter mit dem erforderlichen Ersatzmaterial aufbewahrt. Anschließend wird das geschmolzene Metall in die Form gegossen.
Zur Herstellung des Schalenformsandes wird in der Regel trockener und feiner, völlig tonfreier Sand (90 bis 140 GFN) verwendet. Die zu wählende Korngröße richtet sich nach der gewünschten Oberflächenbeschaffenheit des Gussstücks. Eine zu feine Körnung erfordert eine große Menge an Harz, was die Form teuer macht.
Die beim Schalenformen verwendeten Kunstharze sind im Wesentlichen duroplastische Harze, die durch Hitze irreversibel aushärten. Die am häufigsten verwendeten Harze sind Phenol-Formaldehyd-Harze. In Kombination mit Sand weisen sie eine sehr hohe Festigkeit und Hitzebeständigkeit auf. Bei den beim Schalenformen verwendeten Phenolharzen handelt es sich üblicherweise um zweistufige Harze, das heißt, das Harz enthält überschüssiges Phenol und verhält sich wie ein thermoplastisches Material. Beim Beschichten mit dem Sand wird das Harz mit einem Katalysator wie Hexamethylentetramin (Hexa) in einem Anteil von etwa 14 bis 16 % kombiniert, um die duroplastischen Eigenschaften zu entwickeln. Die Aushärtungstemperatur hierfür würde etwa 150 °C betragen und die erforderliche Zeit würde 50 bis 60 Sekunden betragen.
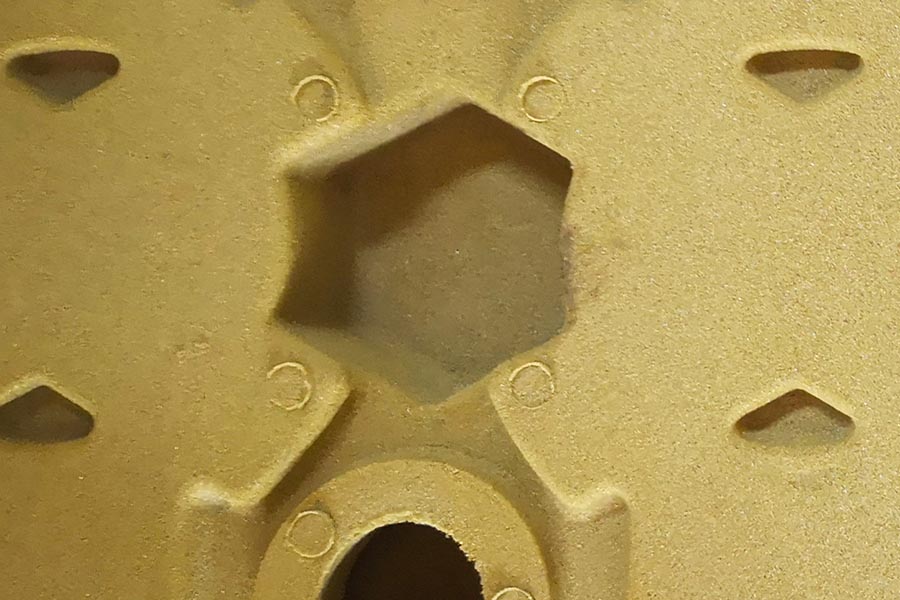
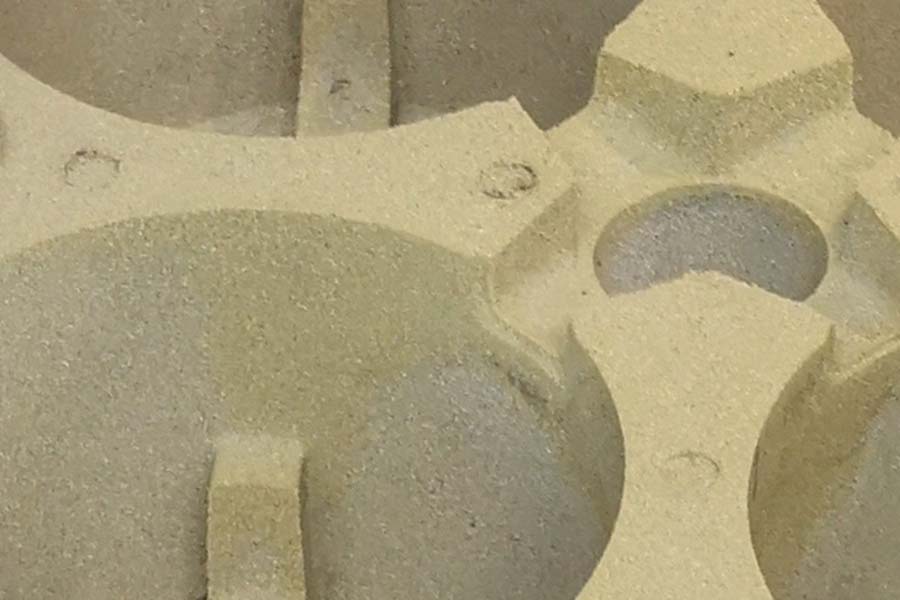
Vorteile des Schalenformgussverfahrens
1.Schalengussteilesind im Allgemeinen maßgenauer als Sandgussteile. Es ist möglich, eine Toleranz von +0,25 mm für Stahlgussteile und +0 mm zu erhalten. 35 mm für Gussteile aus Grauguss undSphärogussteileunter normalen Arbeitsbedingungen. Bei eng tolerierten Schalenformen kann für bestimmte Anwendungen ein Wert im Bereich von +0,03 bis +0,13 mm erreicht werden.
2. Bei Schalengussteilen kann eine glattere Oberfläche erzielt werden. Dies wird vor allem durch die feinere Körnung erreicht. Der typische Rauheitsbereich liegt in der Größenordnung von 3 bis 6 Mikrometern.
3. Formschrägen, die kleiner sind als die Sandgussteile, werden in Schalenformen benötigt. Die Reduzierung der Entformungsschrägen kann zwischen 50 und 75 % betragen, was die Materialkosten und die anschließenden Bearbeitungskosten erheblich einspart.
4. Manchmal kann beim Schalenformen auf spezielle Kerne verzichtet werden. Da der Sand eine hohe Festigkeit aufweist, könnte die Form so gestaltet werden, dass innere Hohlräume direkt geformt werden können, wenn Schalenkerne erforderlich sind.
5. Auch sehr dünne Abschnitte (bis zu 0,25 mm) des Typs luftgekühlter Zylinderköpfe können aufgrund der höheren Festigkeit des zum Formen verwendeten Sandes problemlos durch Schalenformen hergestellt werden.
6. Die Durchlässigkeit der Hülle ist hoch und daher treten keine Gaseinschlüsse auf.
7. Es muss eine sehr kleine Menge Sand verwendet werden.
8. Eine Mechanisierung ist aufgrund der einfachen Verarbeitung beim Schalenformen problemlos möglich.
Einschränkungen des Schalenformgussverfahrens
1. Die Muster sind sehr teuer und daher nur dann wirtschaftlich, wenn sie in Großserien verwendet werden. In einer typischen Anwendung ist das Schalenformen gegenüber dem Sandformen wirtschaftlich, wenn die erforderliche Produktion aufgrund der höheren Modellkosten über 15.000 Stück liegt.
2. Die Größe des durch Schalenformen erhaltenen Gussteils ist begrenzt. Im Allgemeinen können Gussteile mit einem Gewicht von bis zu 200 kg hergestellt werden, in kleineren Mengen werden jedoch auch Gussteile mit einem Gewicht von bis zu 450 kg hergestellt.
3. Es können keine sehr komplizierten Formen erhalten werden.
4. Für die Handhabung der Schalenformteile sind anspruchsvollere Geräte erforderlich, wie sie beispielsweise für erhitzte Metallmodelle erforderlich sind.
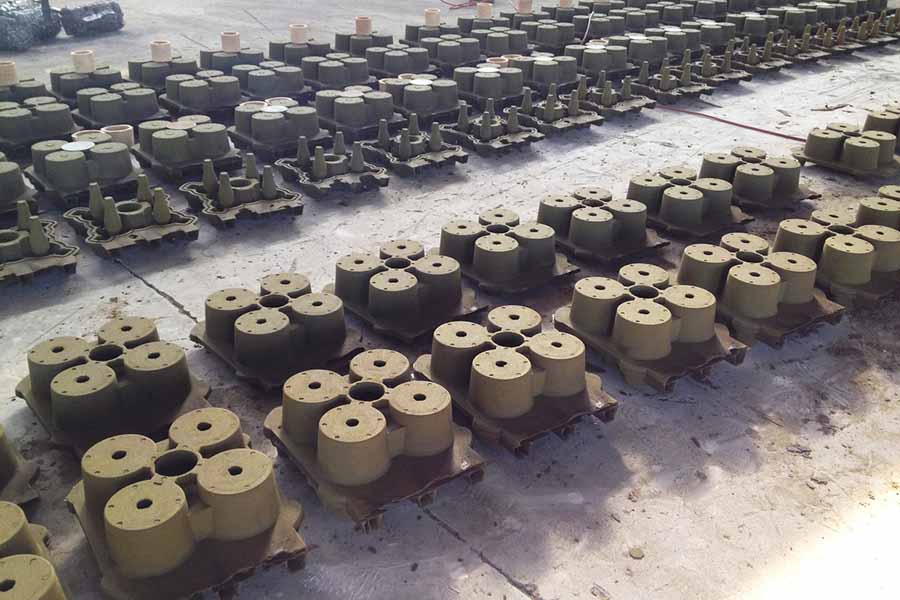
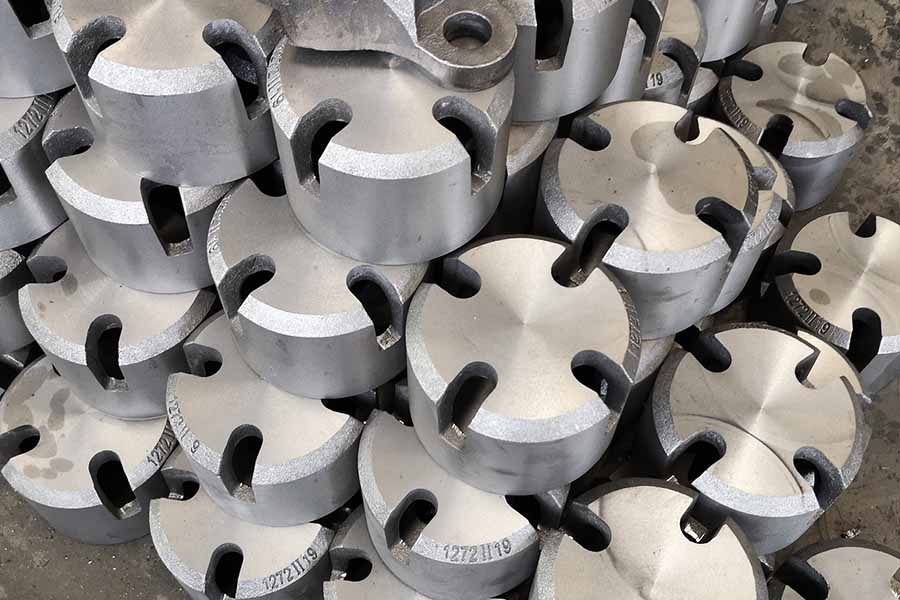
Zeitpunkt der Veröffentlichung: 25. Dezember 2020