Gießerei für Schalenformen
Schalenformguss wird auch als Sandgussverfahren mit vorbeschichtetem Harz, Heißschalenguss oder Kerngussverfahren bezeichnet. Das Hauptformmaterial ist der vorbeschichtete Phenolharzsand, der teurer ist alsgrüner Sandund Furanharzsand. Darüber hinaus kann dieser Sand nicht recycelt werden.
Die Schalenformgusskomponenten haben etwas höhere Kosten alsSandguss. Allerdings ist dieSchalenformgussteilehaben viele Vorteile wie engere Maßtoleranzen, gute Oberflächenqualität und weniger Gussfehler.
Vor der Herstellung der Form und des Kerns wurde der beschichtete Sand mit einem festen Harzfilm auf der Oberfläche der Sandpartikel bedeckt. Der umhüllte Sand wird auch Schalensand (Kernsand) genannt. Der technologische Prozess besteht darin, pulverisiertes duroplastisches Phenolharz mechanisch mit Rohsand zu vermischen und beim Erhitzen zu verfestigen. Es wurde durch die Verwendung von thermoplastischem Phenolharz plus latentem Härter (wie Urotropin) und Gleitmittel (wie Calciumstearat) durch einen bestimmten Beschichtungsprozess zu beschichtetem Sand entwickelt.
Wenn der beschichtete Sand erhitzt wird, schmilzt das auf der Oberfläche der Sandpartikel beschichtete Harz. Unter der Wirkung der durch Maltropin zersetzten Methylengruppe wandelt sich das geschmolzene Harz schnell von einer linearen Struktur in eine unschmelzbare Körperstruktur um, so dass der umhüllte Sand verfestigt und geformt wird. Neben der allgemein trockenen, körnigen Form von beschichtetem Sand gibt es auch nassen und zähflüssigen beschichteten Sand.
Nachdem Sie den Originalsand (oder wiedergewonnenen Sand), das flüssige Harz und den flüssigen Katalysator gleichmäßig gemischt und in den Kernkasten (oder Sandkasten) gefüllt haben, ziehen Sie ihn fest, um ihn in einer Form oder Form im Kernkasten (oder Sandkasten) auszuhärten ) Bei Raumtemperatur wurde die Gussform bzw. der Gusskern geformt, was als selbsthärtende Kaltkern-Kastenmodellierung (Kern) oder selbsthärtende Methode (Kern) bezeichnet wird. Die selbsthärtende Methode kann in die selbsthärtende Methode mit säurekatalysiertem Furanharz und Phenolharzsand, die selbsthärtende Methode mit Urethanharzsand und die selbsthärtende Methode mit Phenolmonoester unterteilt werden.
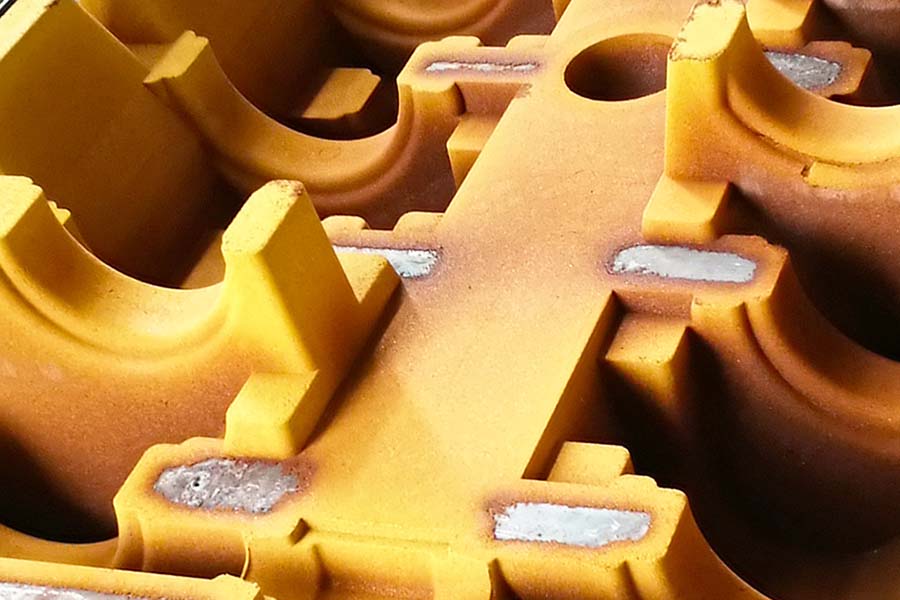
Shell Mould Casting Company
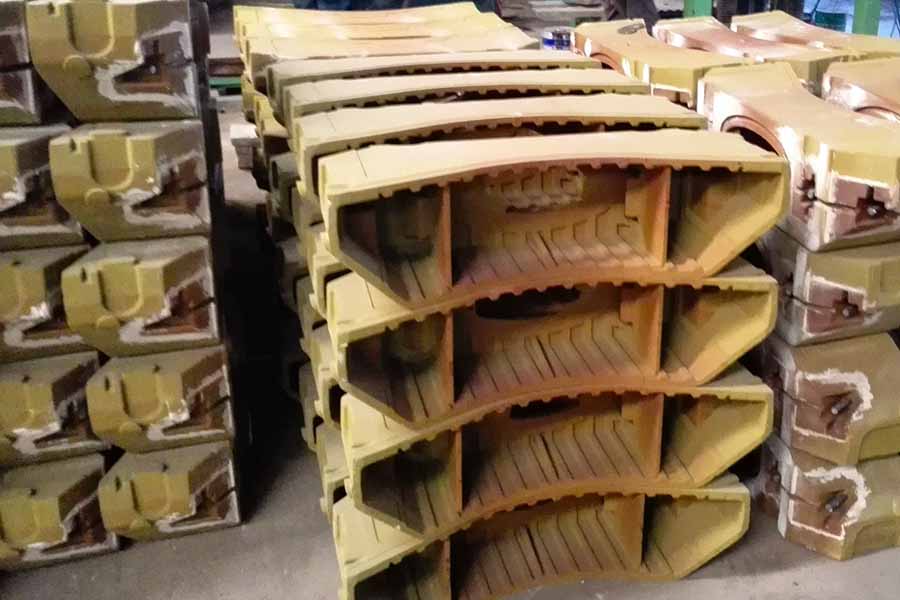
Schalenformguss
Möglichkeiten zum Schalengießen bei RMC Foundry
Bei RMC Foundry können wir die Schalenformgussteile gemäß Ihren Zeichnungen, Anforderungen, Mustern oder einfach nur Ihren Mustern entwerfen und produzieren. Wir könnten die Reverse-Engineering-Dienste anbieten. Derkundenspezifische Gussteileim Schalengussverfahren hergestellt werdendiverse Branchenwie Eisenbahnzüge, schwere Lastkraftwagen, landwirtschaftliche Maschinen,Pumpen und Ventileund Baumaschinen. Im Folgenden finden Sie eine kurze Vorstellung davon, was wir mit dem Schalenformgussverfahren erreichen können:
- • Maximale Größe: 1.000 mm × 800 mm × 500 mm
- • Gewichtsbereich: 0,5 kg – 100 kg
- • Jahreskapazität: 2.000 Tonnen
- • Toleranzen: Auf Anfrage.
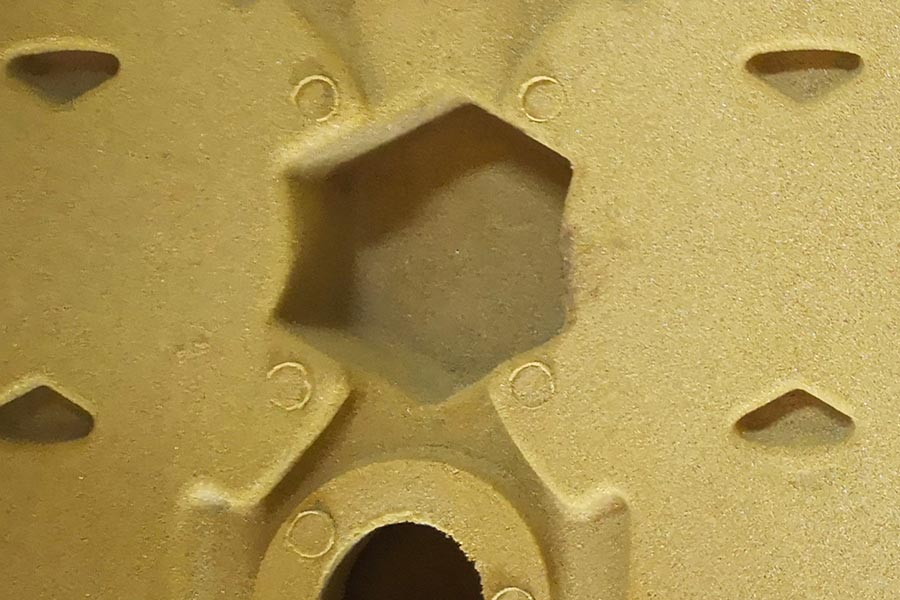
Beschichtete Sandschalenform
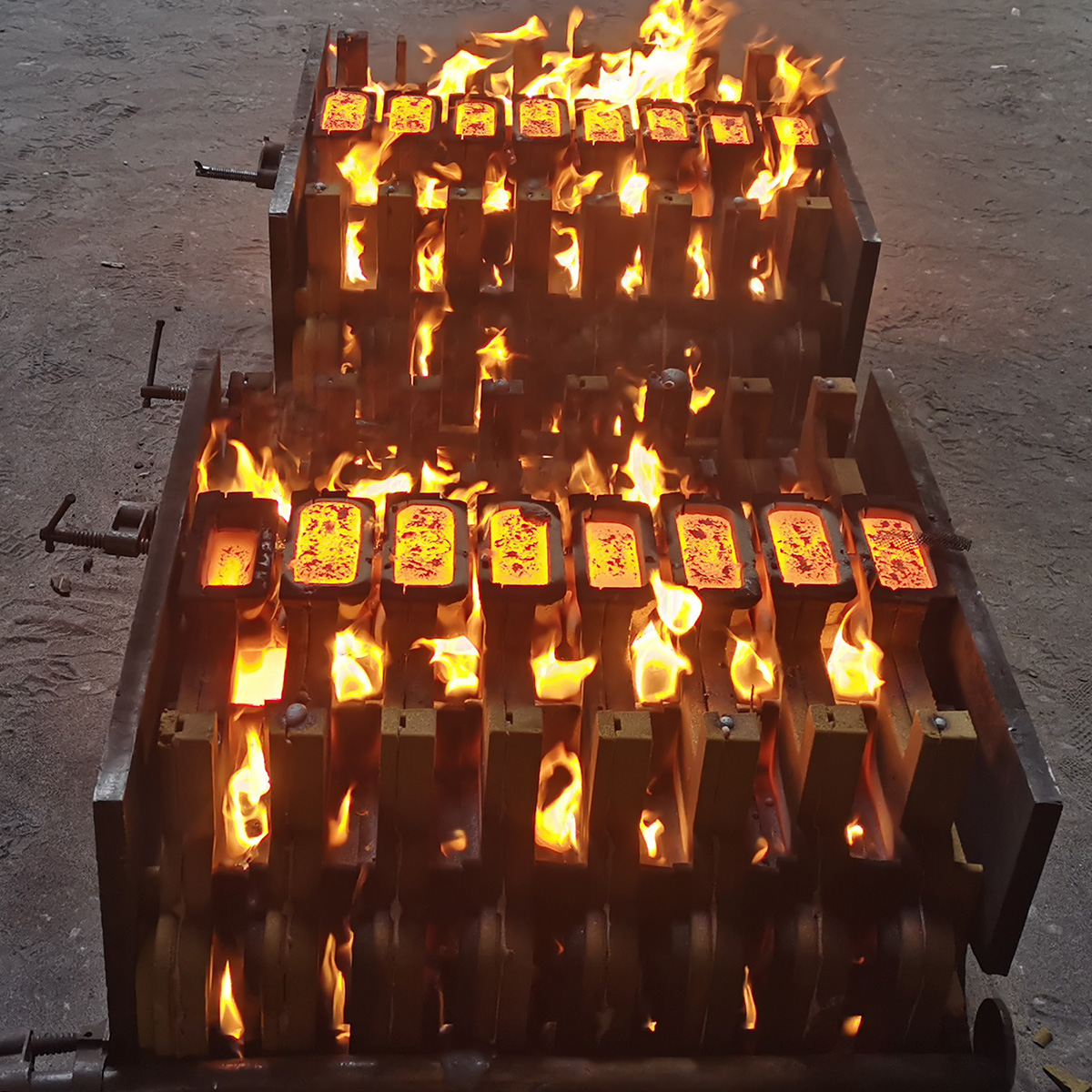
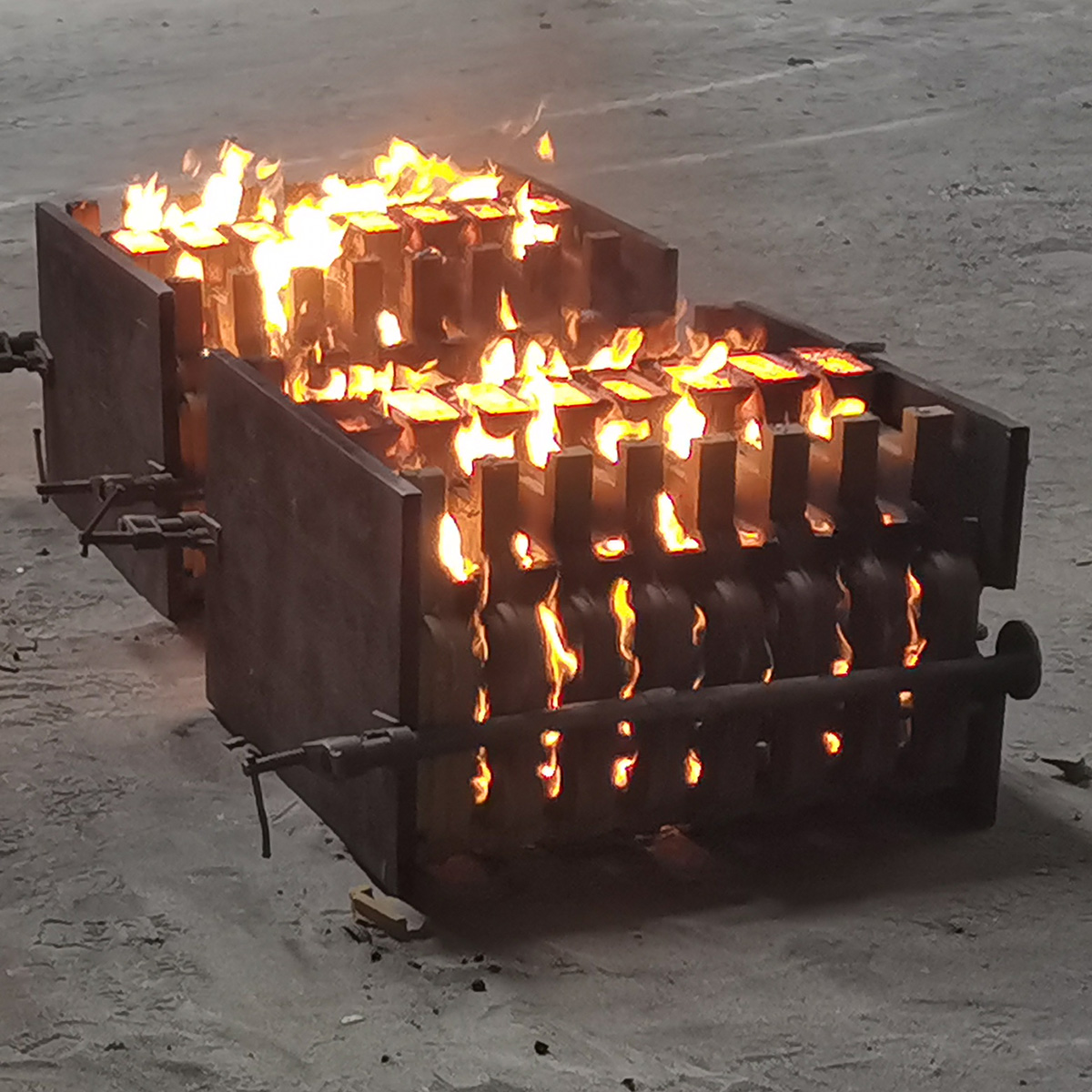
Welche Metalle und Legierungen wir im Schalenformguss gießen
Grauguss,Sphäroguss, Gusskohlenstoffstahl,Gussstahllegierungen,Edelstahlguss,Aluminiumgusslegierungen,Messing und KupferUndAndere Materialien und Standards auf Anfrage.
Metalle und Legierungen | Beliebte Note |
Grauguss | GG10, GG15, GG20, GG25, GG30, GG35 GG40; EN-GJL-100, EN-GJL-150, EN-GJL-200, EN-GJL-250, EN-GJL-300, EN-GJL-350; HT100, HT150, HT200, HT250, HT300, HT350; ASTM A48 Graugusssorten Klasse 20, Klasse 25, Klasse 30, Klasse 35, Klasse 40, Klasse 45, Klasse 50, Klasse 55, Klasse 60. |
Duktiles (kugelförmiges) Gusseisen | GGG40, GGG45, GGG50, GGG55, GGG60, GGG70, GGG80; EN-GJS-400-18, EN-GJS-40-15, EN-GJS-450-10, EN-GJS-500-7, EN-GJS-600-3, EN-GJS-700-2, EN- GJS-800-2; ASTM A536 Duktile Eisensorten 60-40-18, 65-45-12, 70-50-05, 80-60-03, 100-70-03, 120-90-02. |
Austemperiertes duktiles Eisen (ADI) | EN-GJS-800-8, EN-GJS-1000-5, EN-GJS-1200-2 |
Kohlenstoffstahlguss | C20, C25, C30, C45 |
Gusslegierungsstahl | 20Mn, 45Mn, ZG20Cr, 40Cr, 20Mn5, 16CrMo4, 42CrMo, 40CrV, 20CrNiMo, GCr15, 9Mn2V |
Edelstahlguss | Ferritischer Edelstahl, martensitischer Edelstahl, austenitischer Edelstahl, ausscheidungshärtender Edelstahl, Duplex-Edelstahl |
Aluminiumlegierungen | ASTM A356, ASTM A413, ASTM A360 |
Legierungen auf Messing-/Kupferbasis | C21000, C23000, C27000, C34500, C37710, C86500, C87600, C87400, C87800, C52100, C51100 |
Standard: ASTM, SAE, AISI, GOST, DIN, EN, ISO und GB |
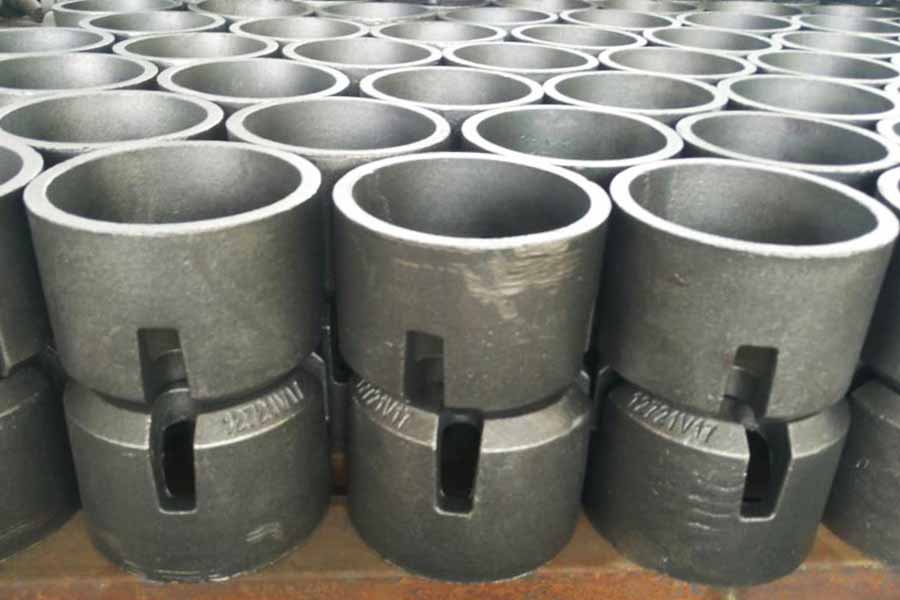
Gussteile aus duktilem Gusseisen
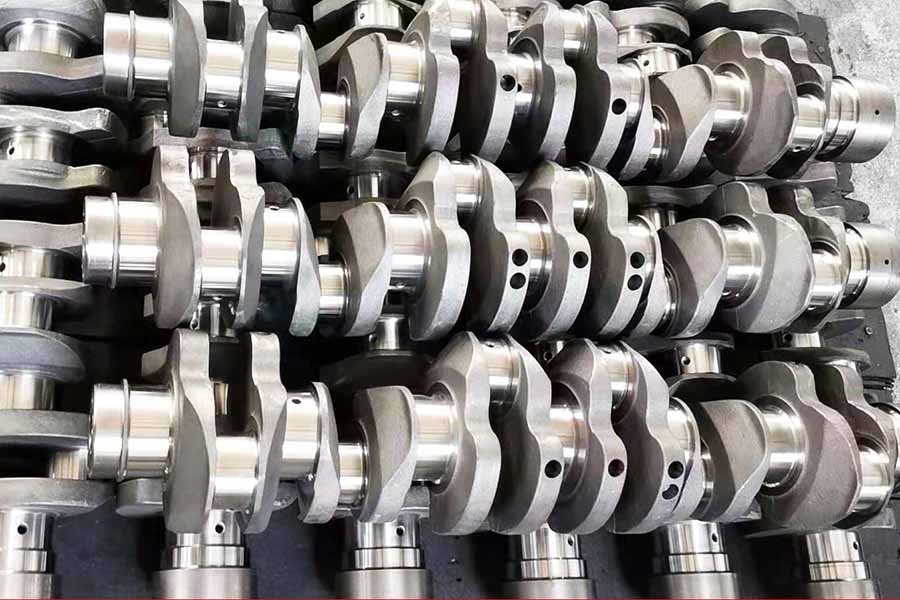
Gussteile aus Sphäroguss
Schritte zum Gießen der Schalenform
✔ Metallmuster herstellen.Der vorbeschichtete Harzsand muss in den Modellen erhitzt werden, daher sind Metallmodelle das notwendige Werkzeug für die Herstellung von Schalengussteilen.
✔ Herstellung einer vorbeschichteten Sandform.Nach der Installation der Metallmodelle auf der Formmaschine wird der vorbeschichtete Harzsand in die Modelle geschossen, und nach dem Erhitzen wird die Harzbeschichtung geschmolzen, dann werden die Sandformen zu festen Sandschalen und Kernen.
✔ Schmelzen des Gussmetalls.Mithilfe von Induktionsöfen würden die Materialien zu einer Flüssigkeit geschmolzen. Anschließend sollte die chemische Zusammensetzung des flüssigen Eisens analysiert werden, um den erforderlichen Zahlen und Prozentsätzen zu entsprechen.
✔ Metall gießen.Wenn das geschmolzene Eisen den Anforderungen entspricht, wird es in die Schalenformen gegossen. Basierend auf unterschiedlichen Charakteristika des Gussdesigns werden die Schalenformen in grünen Sand eingegraben oder schichtweise gestapelt.
✔ Strahlen, Schleifen und Reinigen.Nach dem Abkühlen und Erstarren der Gussteile sollten die Steigrohre, Anschnitte oder zusätzliches Eisen abgeschnitten und entfernt werden. Anschließend werden die Eisengussteile mit Sandstrahlgeräten oder Kugelstrahlmaschinen gereinigt. Nach dem Schleifen des Angusskopfes und der Trennfugen kamen die fertigen Gussteile und warteten bei Bedarf auf die weiteren Prozesse.

Schalenform für Gussteile aus duktilem Eisen
Vorteile des Schalenformgusses
1) Es verfügt über eine geeignete Festigkeitsleistung. Es kann die Anforderungen an hochfesten Schalenkernsand, mittelfesten Hot-Box-Sand und niedrigfesten Nichteisenlegierungssand erfüllen.
2) Hervorragende Fließfähigkeit, gute Formbarkeit des Sandkerns und klare Umrisse, wodurch die komplexesten Sandkerne hergestellt werden können, wie z. B. Sandkerne mit Wassermantel wie Zylinderköpfe und Maschinenkörper.
3) Die Oberflächenqualität des Sandkerns ist gut, kompakt und nicht locker. Selbst wenn weniger oder keine Beschichtung aufgetragen wird, kann eine bessere Oberflächenqualität der Gussteile erzielt werden. Die Maßgenauigkeit von Gussteilen kann Güteklassen von CT 7 bis CT 8 erreichen, und die Oberflächenrauheit Ra kann 6,3 bis 12,5 μm erreichen.
4) Gute Zusammenlegbarkeit, die der Gussreinigung und der Verbesserung der Produktleistung förderlich ist
5) Der Sandkern nimmt Feuchtigkeit nicht leicht auf und die Festigkeit der Langzeitlagerung nimmt nicht leicht ab, was der Lagerung, dem Transport und der Verwendung förderlich ist
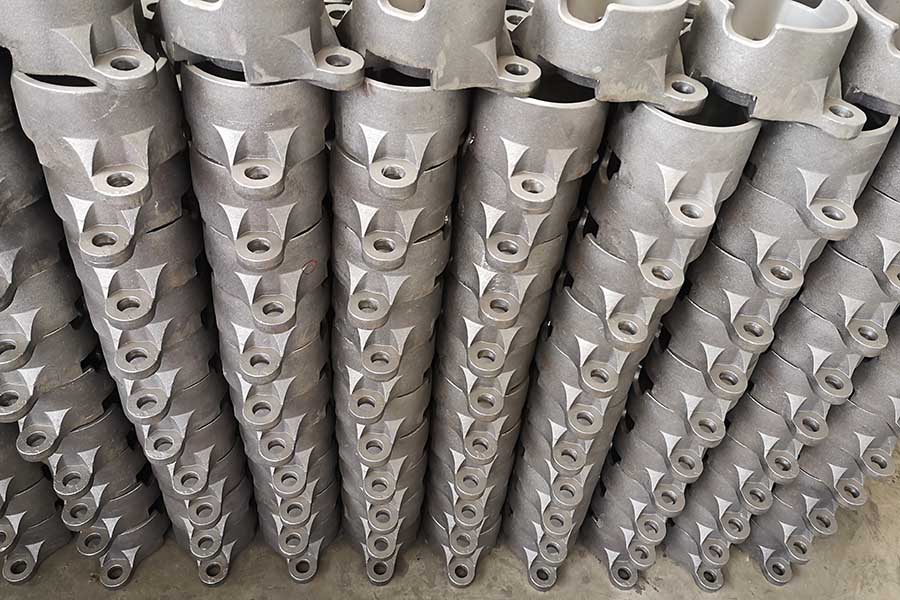
Schalenformgusskomponenten
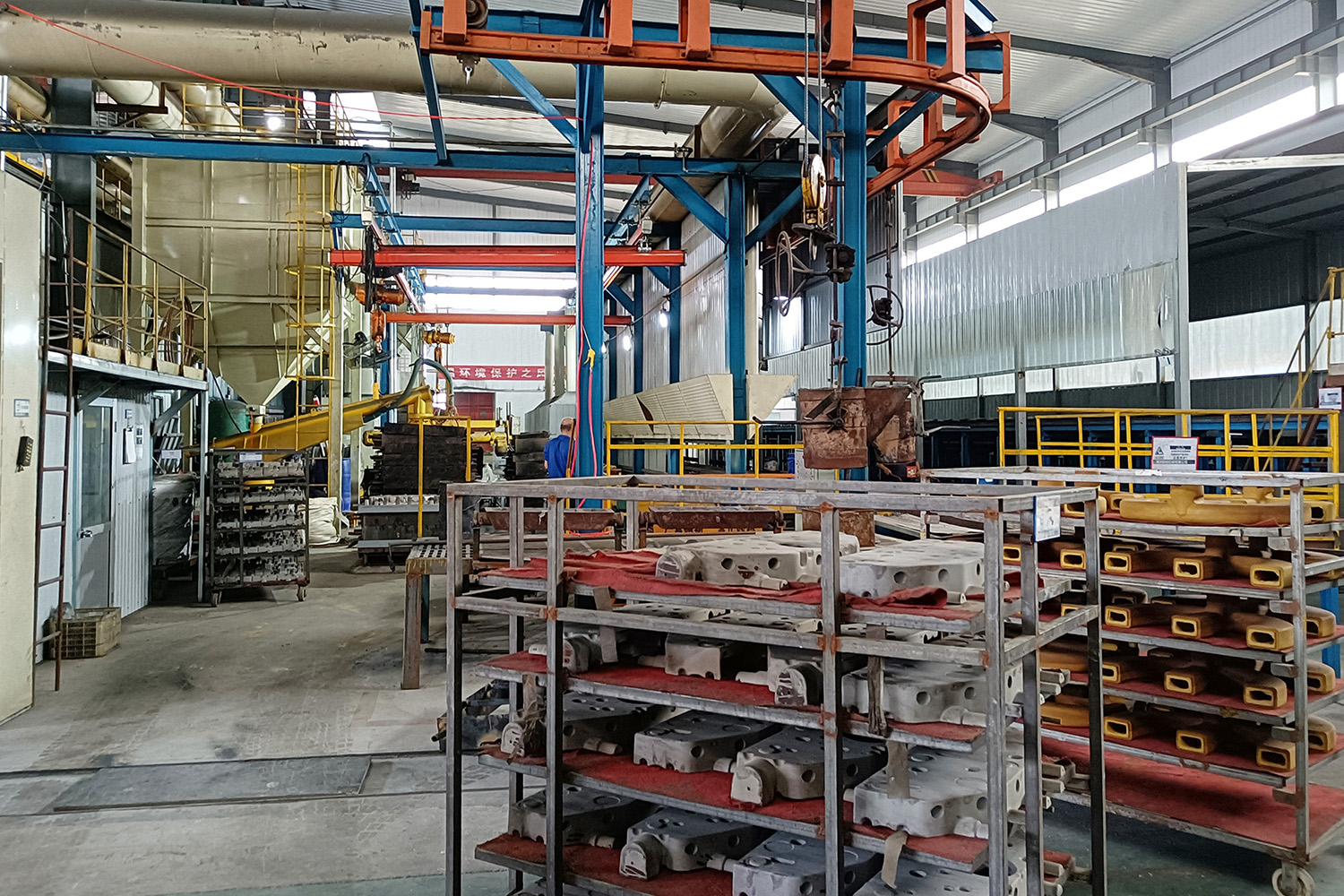
Gießerei für Schalenformen
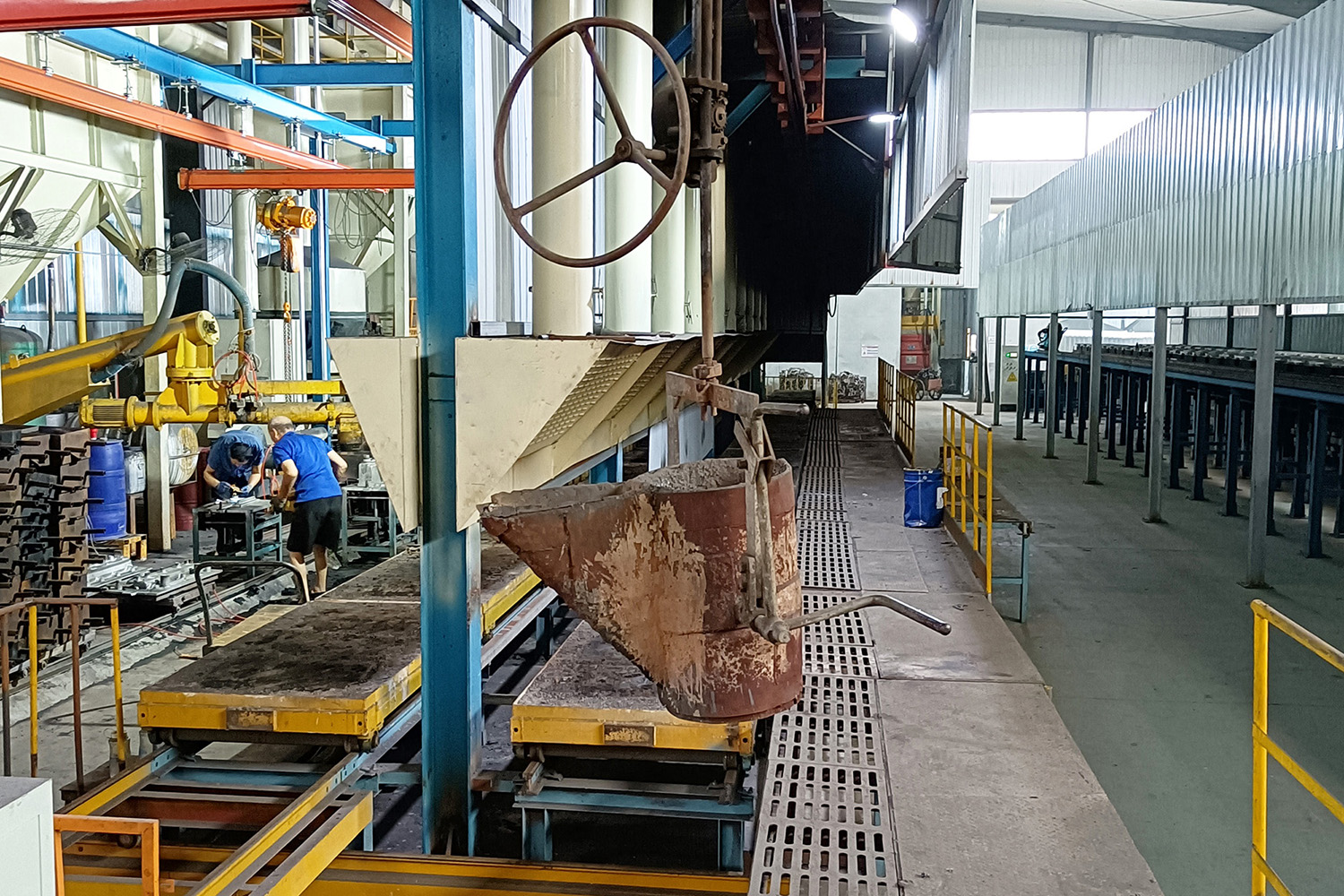
China Steel Foundry
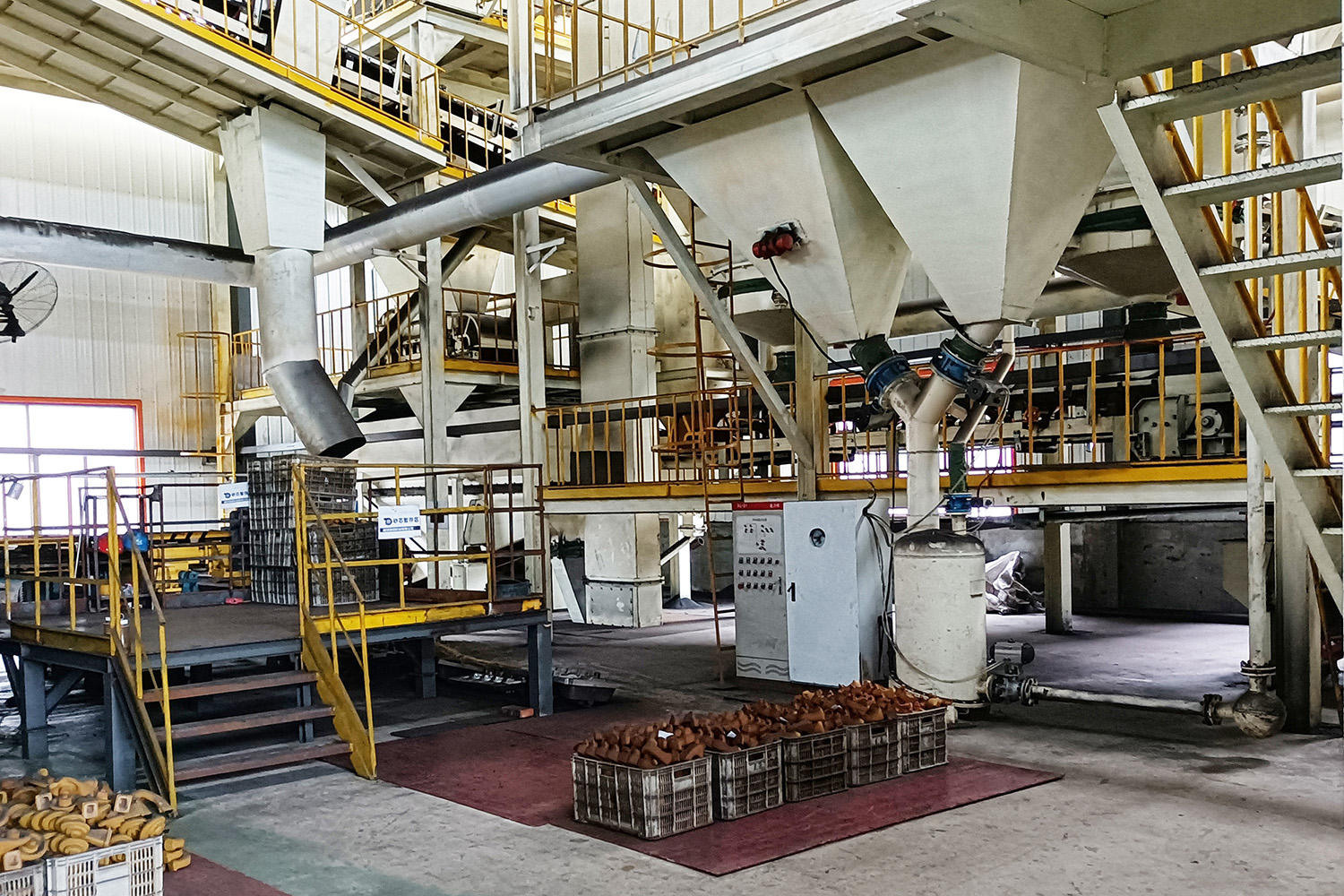
Gusseisengießerei
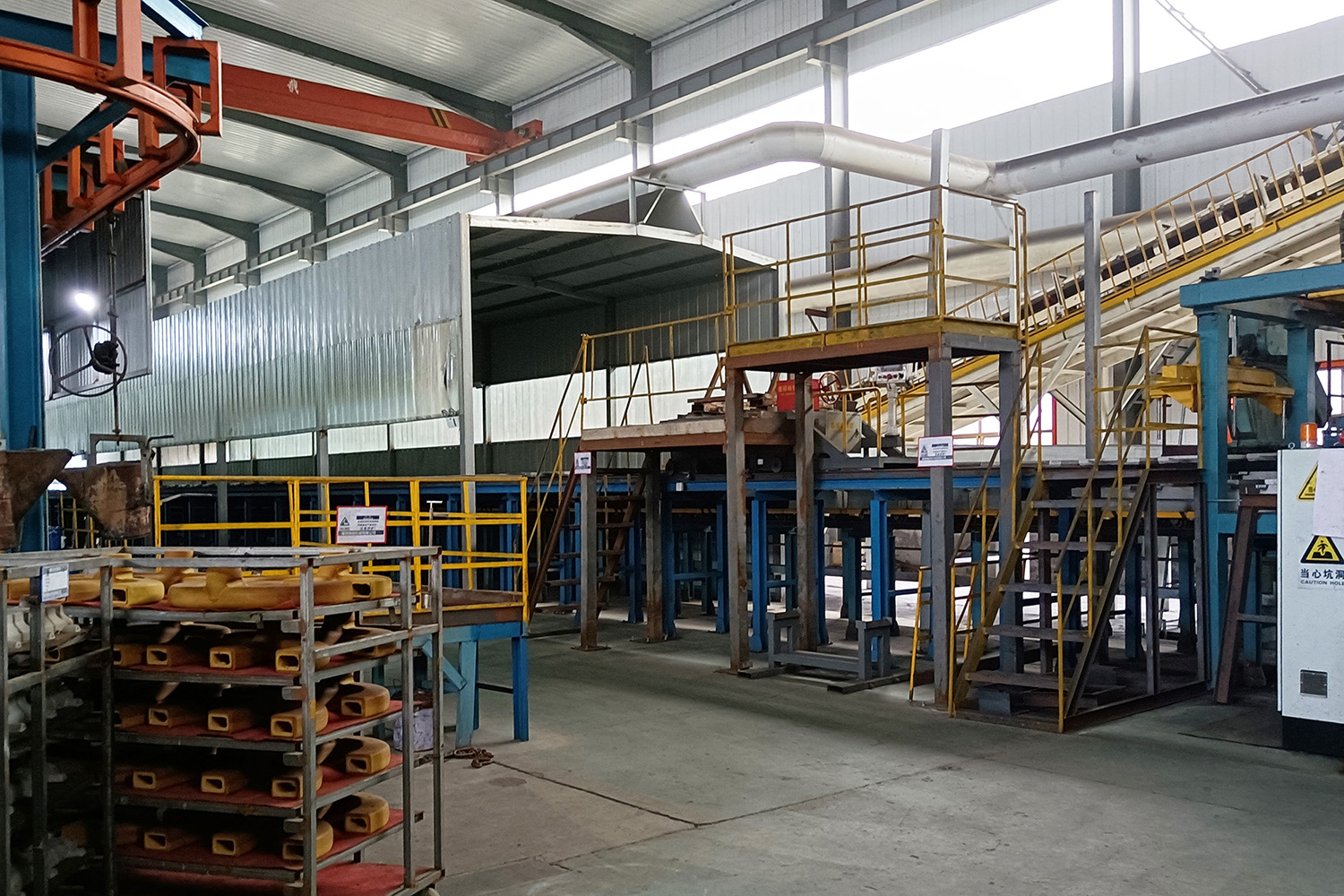
Shell Mould Casting Company
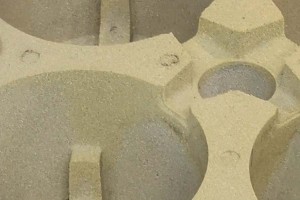
Beschichtete Sandform

Harzbeschichtete Sandform
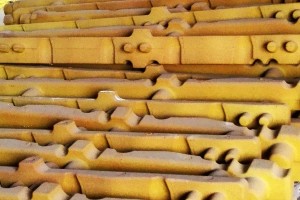
Shell bereit für Gussteile
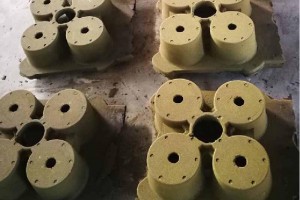
Muschelform ohne Backen
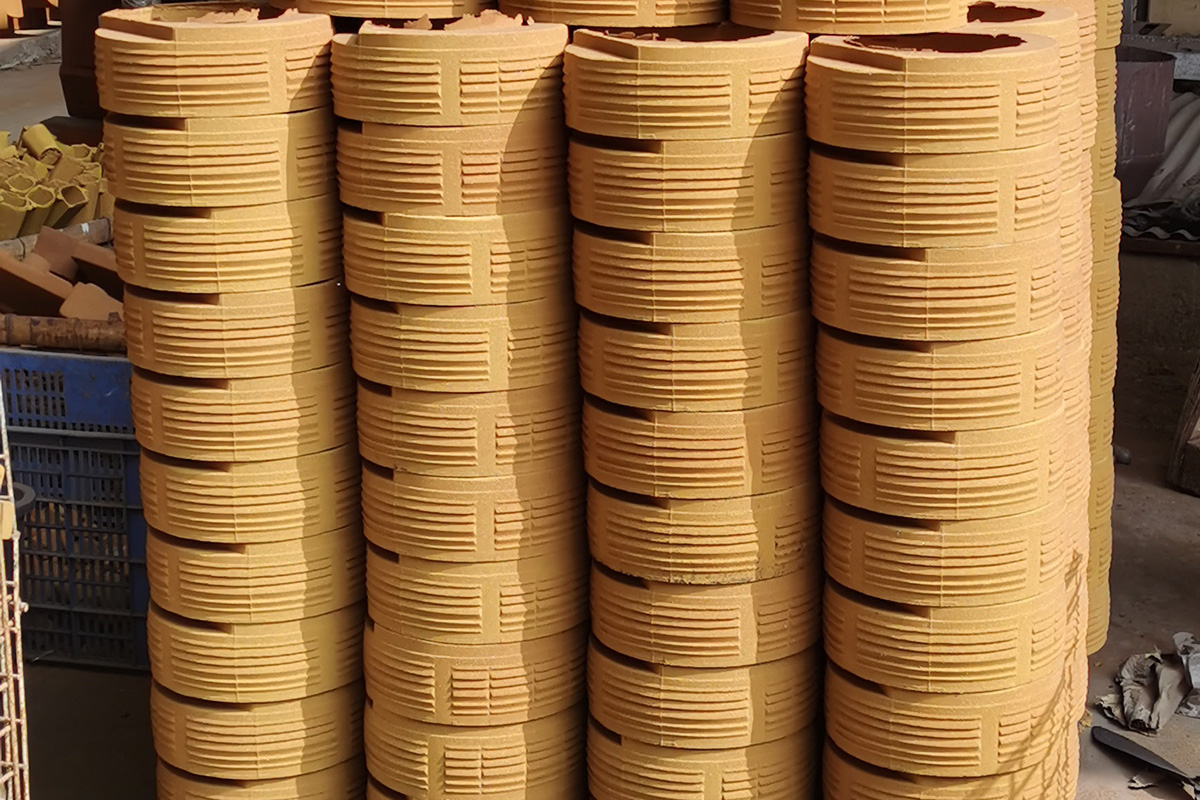
Harzbeschichtete Sandschale
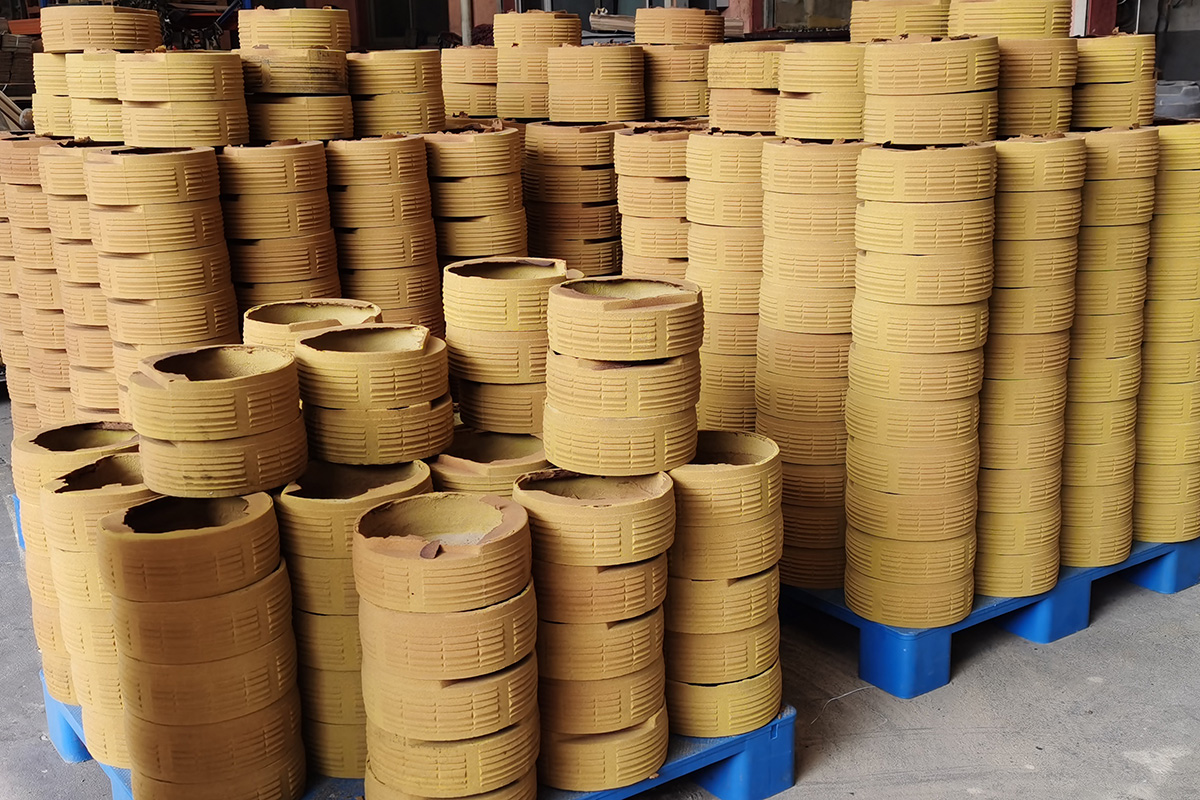
Schalen zum Gießen von geschmolzenem Metall
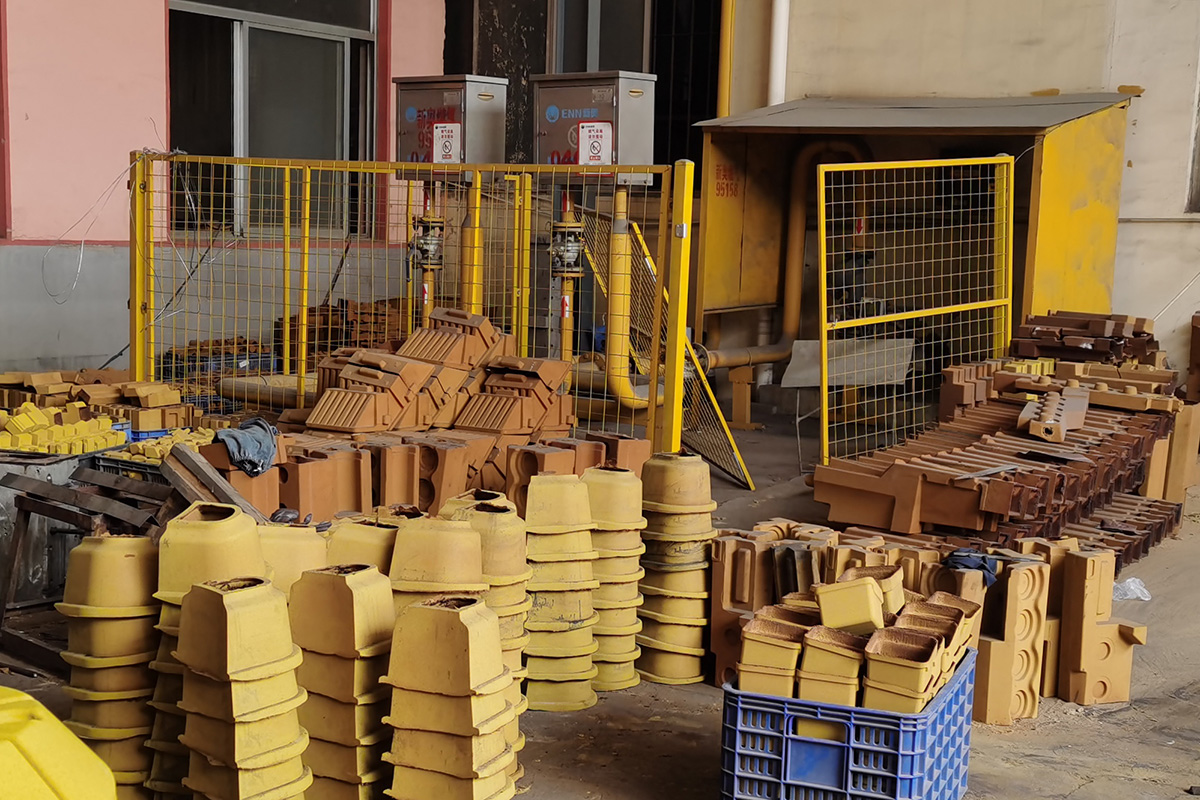
Sandmuschel-Workshop
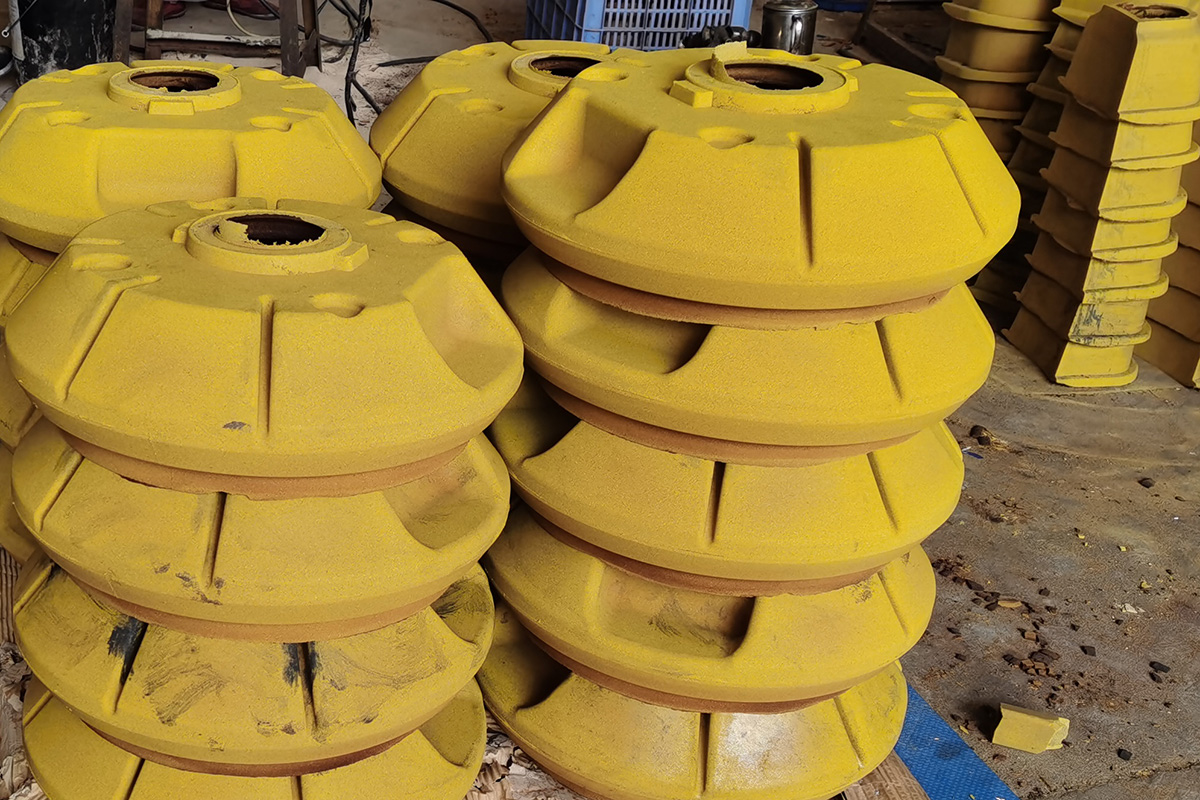
China Shell Foundry
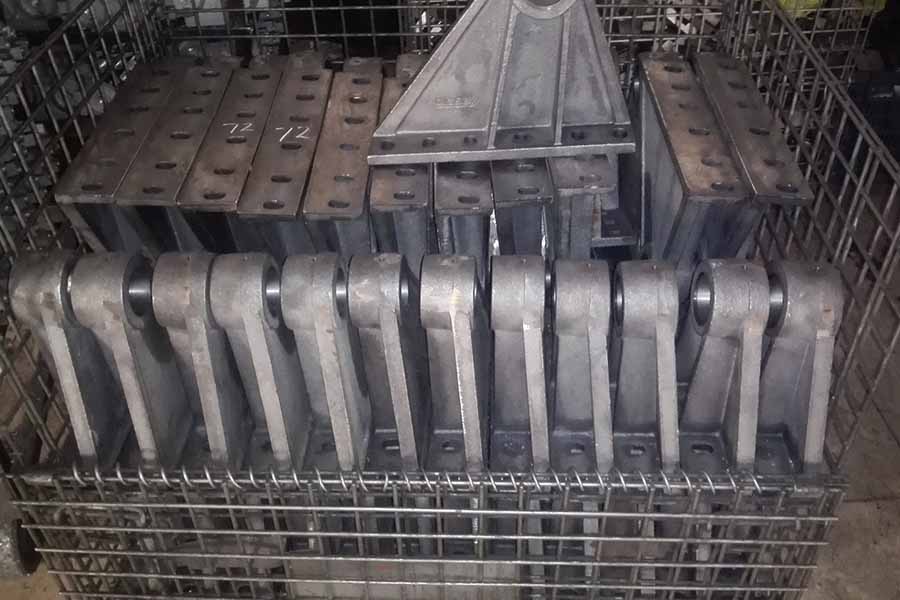
Schalengussprodukte
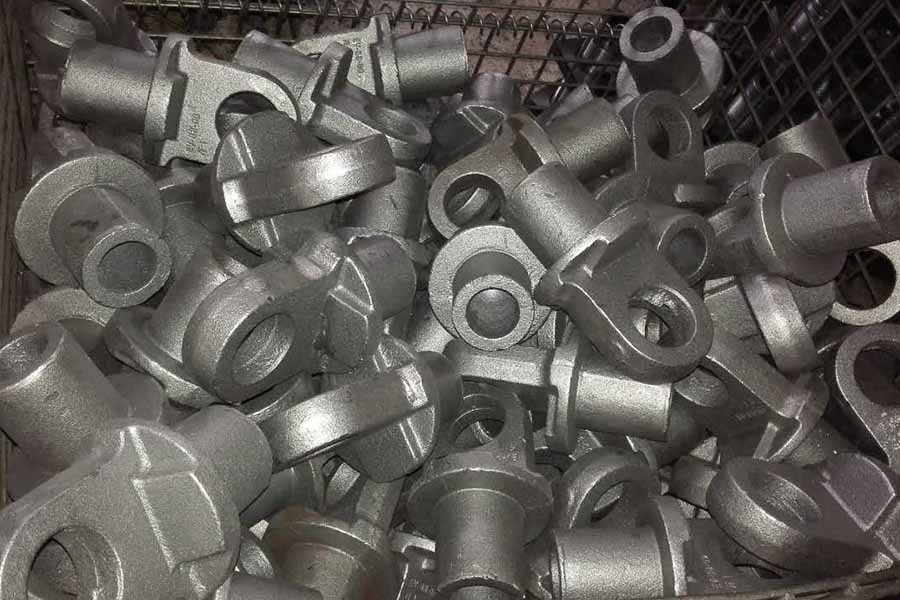
Gussteile aus duktilem Gusseisen
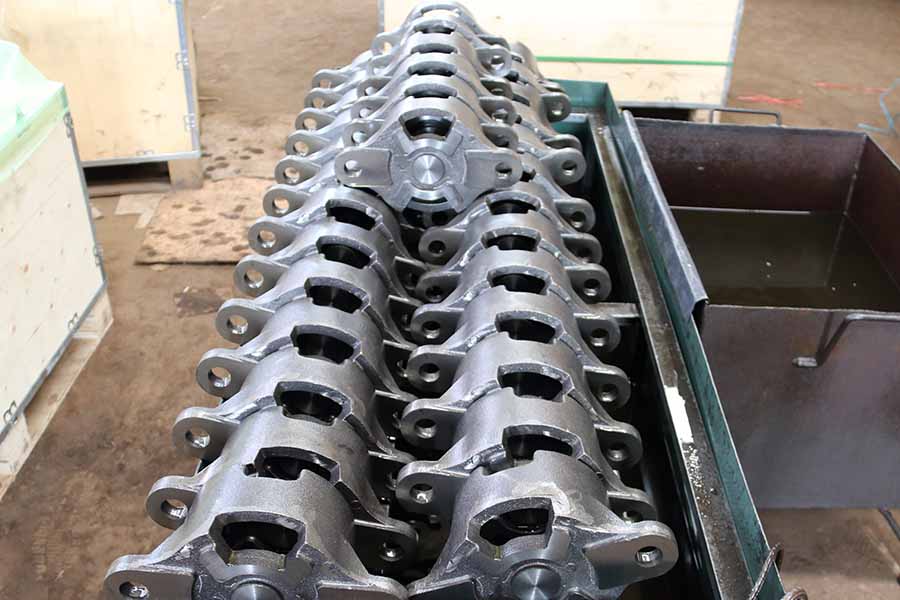
Kundenspezifische Muschelgussteile
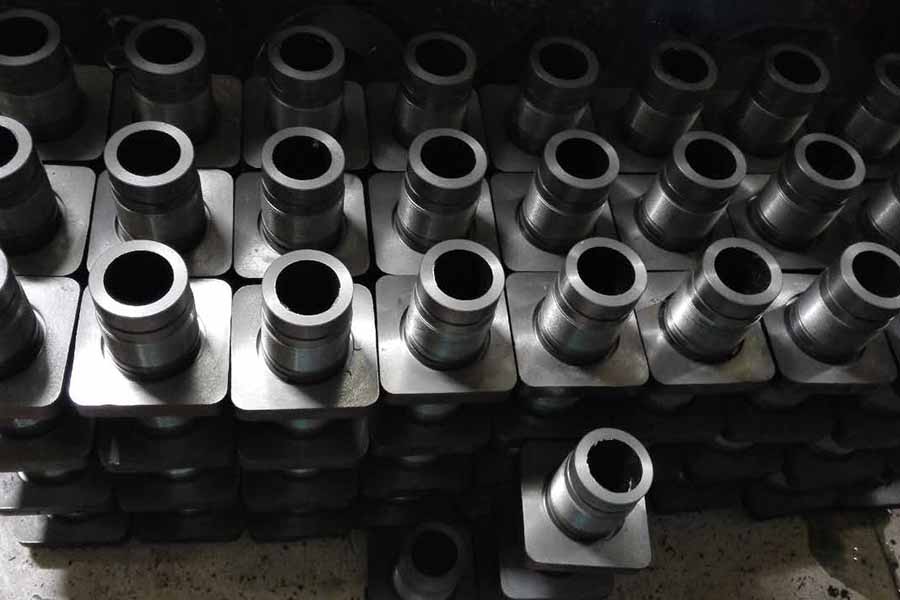
Hydraulikteile für Schalenguss
Kundenspezifische SchalengussteileWir haben produziert
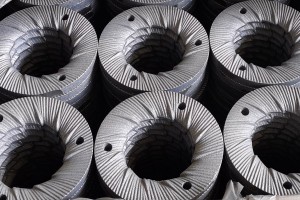
Gussteile aus Grauguss
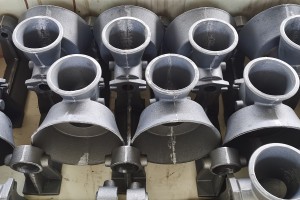
Gusseisengussteile
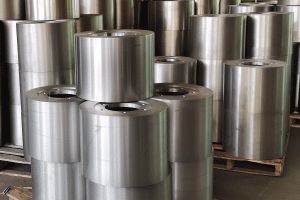
Gussteile aus duktilem Eisen
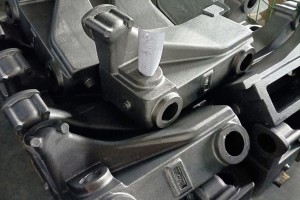
Stahlgussteile durch Schalenformguss
Weitere Dienstleistungen, die wir anbieten könnten
Neben den oben genannten Schalenformgussdiensten können wir auch Folgendes anbietenMehrwertdienstevon Nachgussprozessen. Einige davon werden bei unseren langjährigen Partnern fertiggestellt, andere werden jedoch in unseren hauseigenen Werkstätten hergestellt.
• Entgraten und Reinigen
• Kugelstrahlen/Sandstrahlen
• Wärmebehandlung: Glühen, Normalisieren, Abschrecken, Anlassen, Aufkohlen, Nitrieren
• Oberflächenbehandlung: Passivierung, Andonisieren, Galvanisieren, Heißverzinken, Verzinken, Vernickeln, Polieren, Elektropolieren, Lackieren, GeoMet, Zintec.
•CNC-Bearbeitung: Drehen, Fräsen, Drehen, Bohren, Honen, Schleifen.
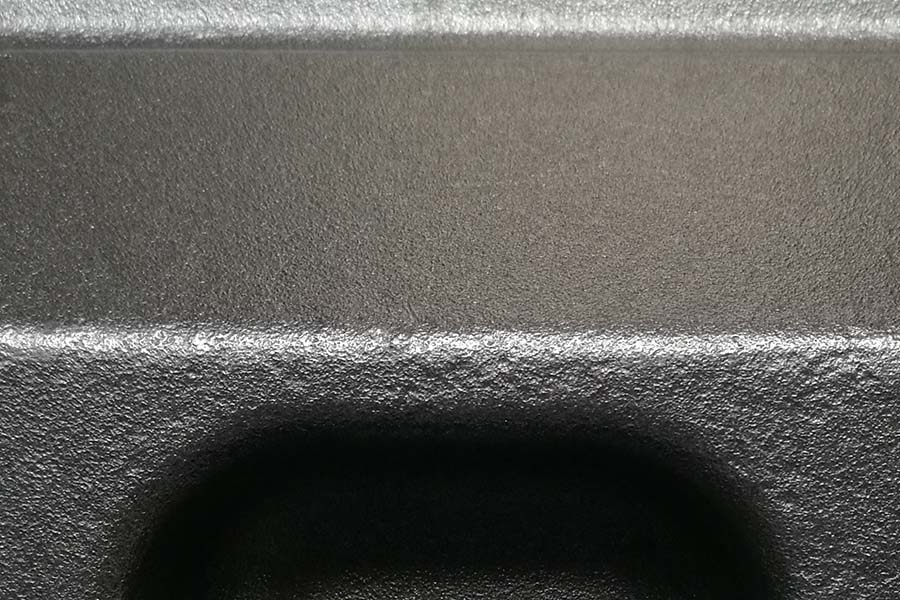