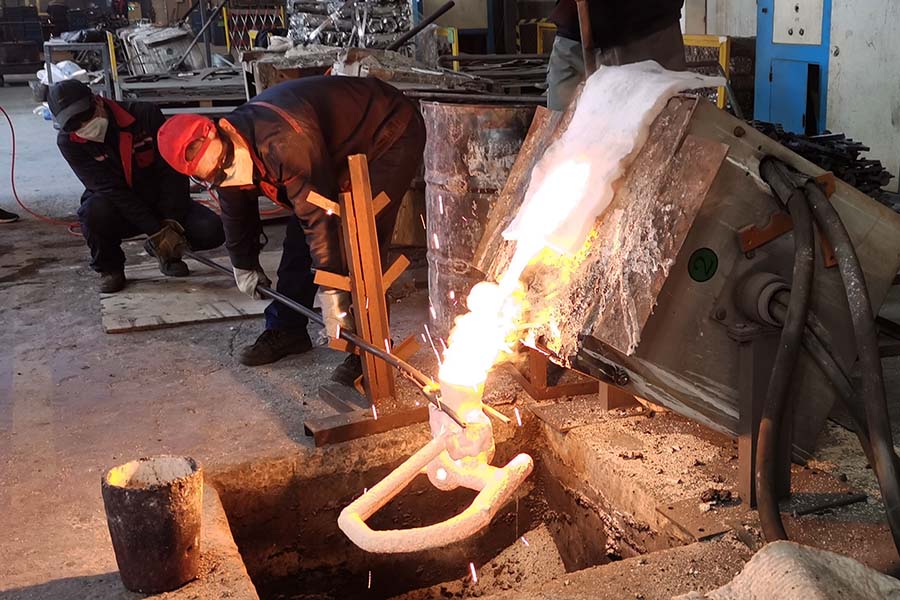
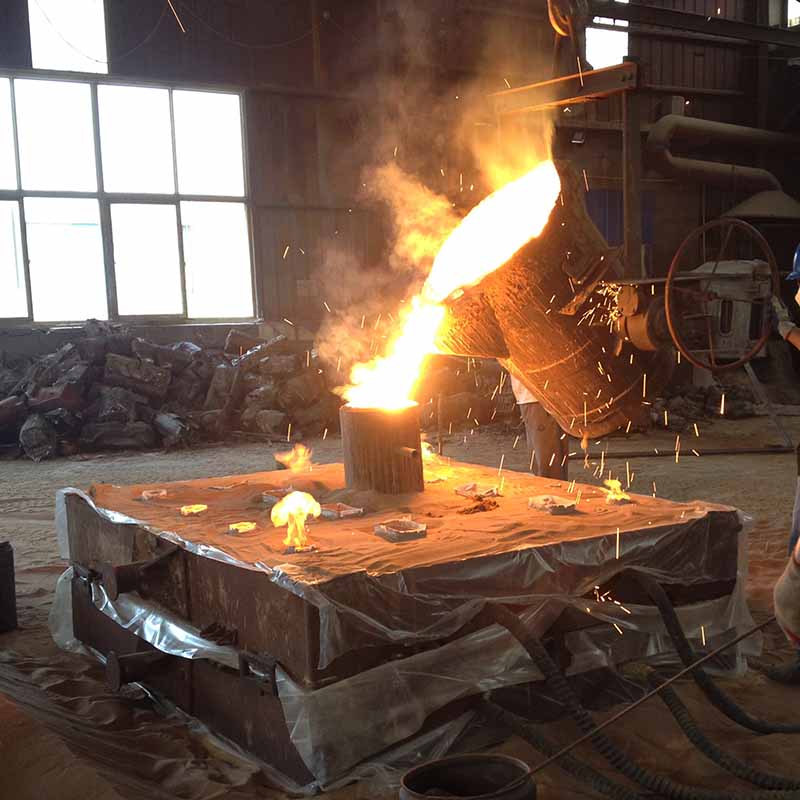
Das Gießen ist eine der frühesten Methoden der Metallumformung, die der Mensch kennt. Dabei handelt es sich im Allgemeinen darum, geschmolzenes Metall in eine feuerfeste Form mit einem Hohlraum der herzustellenden Form zu gießen und es erstarren zu lassen. WannNach dem Erstarren wird der gewünschte Metallgegenstand aus der feuerfesten Form entnommen, indem die Form entweder zerbrochen oder auseinandergenommen wird. Den erstarrten Gegenstand nennt man Guss. Dieser Prozess wird auch als Gründung bezeichnet, und die moderne Fabrik, die sich auf das Gießen von Metallteilen konzentriert, wird auch genanntGießerei.
1. Geschichte des Gießprozesses
Das Gussverfahren wurde vermutlich um ca. 3500 v. Chr. in Mesopotamien entdeckt. In vielen Teilen der Welt wurden zu dieser Zeit Kupferäxte und andere flache Gegenstände in offenen Formen aus Stein hergestellt oder gebackenTon. Diese Formen bestanden im Wesentlichen aus einem Stück. Aber in späteren Zeiten, als runde Gegenstände hergestellt werden mussten, wurden solche Formen in zwei oder mehr Teile geteilt, um das Herausnehmen der runden Gegenstände zu erleichternDie Bronzezeit (ca. 2000 v. Chr.) brachte weitaus mehr Verfeinerung in den Gussprozess. Möglicherweise wurde zum ersten Mal ein Kern zur Herstellung von Hohltaschen in den Gegenständen erfunden. Diese Kerne wurden aus gebranntem Ton hergestellt.Auch das Cire Perdue- oder Wachsausschmelzverfahren wurde häufig zur Herstellung von Ornamenten und feinen Arbeiten eingesetzt.
Die Gusstechnik wurde ab etwa 1500 v. Chr. von den Chinesen stark verbessert. Zuvor gab es keine Hinweise auf Casting-Aktivitäten in China. Sie scheinen nicht großartig gewesen zu seinEr war mit dem Cire-Perdue-Verfahren vertraut und nutzte es auch nicht ausgiebig, sondern spezialisierte sich stattdessen auf mehrteilige Formen für die Herstellung äußerst komplizierter Arbeiten. Sie haben viel Zeit damit verbracht, die Form bis ins letzte Detail zu perfektionieren, so dass kaum etwas passiertAm aus den Formen hergestellten Guss waren noch Nacharbeiten erforderlich. Wahrscheinlich stellten sie Stückformen her, die sorgfältig zusammengefügte Stücke enthielten und deren Anzahl dreißig oder mehr betrug. Tatsächlich wurden viele solcher Formen ausgegrabenWährend archäologischer Ausgrabungen in verschiedenen Teilen Chinas.
Die Industal-Zivilisation ist auch für die weit verbreitete Verwendung von Kupfer- und Bronzeguss für Schmuck, Waffen, Werkzeuge und Gebrauchsgegenstände bekannt. Aber es gab keine großen Verbesserungen in der Technologie. Aus der VariBei vielen Objekten und Figuren, die an den Stätten im Indus-Tal ausgegraben wurden, scheinen sie mit allen bekannten Gussmethoden wie der offenen Form, der Stückform und dem Cire-Perdue-Verfahren vertraut gewesen zu sein.
Obwohl Indien die Erfindung des Tiegelstahls zu verdanken hat, gab es in Indien nicht viel von der Eisengießerei. Es gibt Hinweise darauf, dass die Eisengießerei um 1000 v. Chr. in Syrien und Persien begann. Es erscheintDasEisengussTechnologie wird in Indien seit der Invasion Alexanders des Großen um 300 v. Chr. eingesetzt.
Die berühmte Eisensäule, die sich heute in der Nähe des Qutb-Minar in Delhi befindet, ist ein Beispiel für die metallurgischen Fähigkeiten der alten Inder. Es ist 7,2 m lang und besteht aus reinem Temperguss. Es wird davon ausgegangen, dass dies der Fall istZeit von Chandragupta II. (375-413 n. Chr.) aus der Gupta-Dynastie. Die Rostrate dieser Säule, die draußen im Freien steht, ist praktisch Null und selbst der vergrabene Teil rostet extrem langsam. Dasmuss zuerst gegossen und dann in die endgültige Form gehämmert worden sein.
2. Vorteile und Einschränkungen
Aufgrund seiner vielen Vorteile wird das Gießverfahren häufig in der Fertigung eingesetzt. Geschmolzenes Material fließt in jeden kleinen Abschnitt im Formhohlraum und somit in jede komplizierte Form – im Innerenoder extern – können im Gussverfahren hergestellt werden. Es ist möglich, praktisch jedes Material zu gießen, egal ob Eisen oder Nichteisen. Darüber hinaus sind die zum Gießen von Formen erforderlichen Werkzeuge sehr einfach undpreiswert. Daher ist es für die Probeproduktion oder die Produktion einer kleinen Menge eine ideale Methode. Beim Gussverfahren ist es möglich, die Materialmenge genau dort zu platzieren, wo sie benötigt wird. InfolgeGewichtsreduzierung im Design kann erreicht werden.Castingswerden im Allgemeinen von allen Seiten gleichmäßig gekühlt und daher wird erwartet, dass sie keine Richtungseigenschaften haben. Es gibt bestimmte Metalle und Legierungendie aus metallurgischen Gründen nur durch Gießen und nicht durch ein anderes Verfahren wie Schmieden verarbeitet werden kann. Es können Gussteile jeder Größe und jedes Gewichts, sogar bis zu 200 Tonnen, hergestellt werden.
Allerdings sind Maßhaltigkeit und Oberflächenbeschaffenheit normalSandgussverfahrenwäre in vielen Fällen für eine endgültige Anwendung nicht ausreichend. Um diese Fälle zu berücksichtigen, gibt es einige spezielle GussteileEs wurden Verfahren wie das Druckgießen entwickelt, deren Einzelheiten in späteren Kapiteln beschrieben werden. Außerdem ist der Sandgussprozess bis zu einem gewissen Grad arbeitsintensiv und daher zielen viele Verbesserungen darauf ab.wie maschinelles Formen und Gießereimechanisierung. Bei einigen Materialien ist es oft schwierig, Mängel zu beseitigen, die auf die darin enthaltene Feuchtigkeit zurückzuführen sindSandgussteile.
3. Casting-Bedingungen
In den folgenden Kapiteln werden die Einzelheiten des Sandgusses erläutert, der den Grundprozess des Gießens darstellt. Bevor wir auf die Einzelheiten des Prozesses eingehen, sollten wir eine Reihe von Vokabeln für die Besetzung definierengeeignet.
Flasche– Ein Formbehälter ist ein Behälter, der die Sandform intakt hält. Abhängig von der Position des Kolbens in der Formstruktur wird er mit verschiedenen Namen wie „Drag“, „Cope“ und „Wange“ bezeichnet. Es besteht aus Holzfür temporäre Anwendungen oder allgemeiner aus Metall für den Langzeitgebrauch.
Ziehen– Formkasten absenken
Bewältigen– Oberer Formkasten
Wange– Zwischenformkasten für das Formen von drei Teilen.
Muster– Muster ist eine Nachbildung des endgültigen Objekts, das mit einigen Änderungen hergestellt werden soll. Mit Hilfe des Musters wird der Formhohlraum hergestellt.
Trennlinie– Dies ist die Trennlinie zwischen den beiden Formkästen, aus denen die Sandform besteht. Beim geteilten Muster ist es auch die Trennlinie zwischen den beiden Hälften des Musters
Unteres Brett– Dies ist ein normalerweise aus Holz gefertigtes Brett, das zu Beginn des Formenbaus verwendet wird. Das Muster wird zunächst auf dem Bodenbrett festgehalten, Sand wird darauf gestreut und dann erfolgt das Stampfen in der Schleppe.
Mit Blick auf Sand– Die kleine Menge kohlenstoffhaltigen Materials wird auf die Innenfläche des Formhohlraums gestreut, um den Gussteilen eine bessere Oberflächenbeschaffenheit zu verleihen
Formsand– Es handelt sich um das frisch zubereitete feuerfeste Material, das zur Herstellung des Formhohlraums verwendet wird. Es handelt sich um eine Mischung aus Quarzton und Feuchtigkeit in geeigneten Anteilen, um die gewünschten Ergebnisse zu erzielen, und umgibt die HautMuster beim Herstellen der Form.
Untergrundsand– Es ist das, was den größten Teil des feuerfesten Materials in der Form ausmacht. Dieser besteht aus gebrauchtem und verbranntem Sand.
Kern– Es wird zur Herstellung von Hohlräumen in Gussteilen verwendet.
Ausgießbecken– Ein kleiner trichterförmiger Hohlraum oben in der Form, in den das geschmolzene Metall gegossen wird.
Spur– Der Durchgang, durch den das geschmolzene Metall aus dem Gießbecken in den Formhohlraum gelangt. In vielen Fällen steuert es den Metallfluss in die Form.
Läufer– Die Durchgänge in der Trennebene, durch die der Fluss des geschmolzenen Metalls reguliert wird, bevor es den Formhohlraum erreicht.
Tor– Der eigentliche Eintrittspunkt, durch den geschmolzenes Metall in den Formhohlraum gelangt.
Kranz– Chaplets werden verwendet, um Kerne im Formhohlraum zu stützen, um ihr Eigengewicht zu tragen und die metallostatischen Kräfte zu überwinden.
Kühlen– Kühlkörper sind metallische Gegenstände, die in die Form gelegt werden, um die Abkühlgeschwindigkeit von Gussteilen zu erhöhen und eine gleichmäßige oder gewünschte Abkühlgeschwindigkeit zu erreichen.
Steigleitung– Dabei handelt es sich um ein im Gussteil vorgesehenes Reservoir für geschmolzenes Metall, sodass heißes Metall in den Formhohlraum zurückfließen kann, wenn das Metallvolumen aufgrund der Erstarrung abnimmt
4. Verfahren zur Herstellung von Sandformen
Das Verfahren zur Herstellung einer typischen Sandform wird in den folgenden Schritten beschrieben:
Zunächst wird eine Bodenplatte entweder auf die Formplattform oder auf den Boden gelegt, um die Oberfläche eben zu machen. Der Schleppformkolben wird zusammen mit dem Schleppteil des Schleppformkolbens kopfüber auf der Bodenplatte gehaltenMuster in der Mitte des Kolbens auf der Tafel. Zwischen dem Muster und den Wänden des Kolbens sollte ein ausreichender Abstand vorhanden sein, der in der Größenordnung von 50 bis 100 mm liegen sollte. Trockener Vorsatzsand wird darüber gestreutdas Brett und das Muster, um eine nicht klebrige Schicht zu schaffen. Nun wird frisch aufbereiteter Formsand der erforderlichen Qualität in einer Dicke von 30 bis 50 mm in die Schleppe und auf das Modell gegossen. Der Rest des Schleppkolbens istvollständig mit dem Stützsand gefüllt und gleichmäßig gerammt, um den Sand zu verdichten. Das Stampfen des Sandes sollte ordnungsgemäß erfolgen, um ihn nicht zu stark zu verdichten, was das Entweichen von Gasen erschwert.noch zu locker, so dass die Form nicht genügend Festigkeit hätte. Nach Abschluss des Stampfvorgangs wird der überschüssige Sand im Behälter mit einem Flacheisen vollständig bis auf Höhe der Behälterränder abgekratzt.
Nun werden mit einem Entlüftungsdraht, einem Draht mit einem Durchmesser von 1 bis 2 mm und einem spitzen Ende, Entlüftungslöcher in die gesamte Tiefe des Kolbens sowie in das Muster eingebracht, um die Entfernung von Gasen zu erleichtern beim GießenErstarrung. Damit ist die Vorbereitung des Drags abgeschlossen.
Der fertige Ziehkolben wird nun auf die Bodenplatte gerollt, wodurch das Muster freigelegt wird, wie auf dem Foto gezeigt. Mit einem Slick werden die Sandkanten rund um das Muster ausgebessert und die obere Hälfte des Musters darüber gelegtdas Schleppmuster und richten es mit Hilfe von Passstiften aus. Der Oberkasten oben auf der Bremse wird mit Hilfe der Stifte wieder ausgerichtet. Der trockene Trennsand wird über die gesamte Schleppe und das Muster gestreut.
In einem geringen Abstand von etwa 50 mm vom Modell befindet sich ein Angussstift zur Herstellung des Angusskanals. Außerdem wird der Steigungsstift bei Bedarf an einem geeigneten Ort aufbewahrt und frisch zubereiteter Formsand ähnlichDer Schleppsand wird zusammen mit dem Trägersand aufgestreut. Der Sand wird gründlich gerammt, überschüssiger Sand abgekratzt und überall in der Oberkante wie in der Schleppe werden Entlüftungslöcher angebracht.
Der Angussstift und der E-Riser-Stift werden vorsichtig aus dem Kolben herausgezogen. Später wird das Gießbecken nahe der Oberseite des Angusses eingeschnitten. Der Oberkasten wird von der Bremse und jeglichem losen Sand auf der Schnittstelle zwischen Oberkasten und Bremse getrenntDer Luftwiderstand wird mit Hilfe eines Blasebalgs abgeblasen. Nun werden die Oberkasten- und Schleppmodellhälften herausgezogen, indem die Ziehdorne verwendet und das Modell rundherum geklopft werden, um den Formhohlraum leicht zu vergrößern, so dass die Form leicht vergrößert wirdSchimmelwände werden durch das zurückziehende Muster nicht beschädigt. Die Angusskanäle und Anschnitte werden sorgfältig in die Form geschnitten, ohne die Form zu beschädigen. Überschüssiger oder loser Sand, der sich in den Angusskanälen und im Formhohlraum befindet, wird weggeblasenmit dem Blasebalg weg. Nun wird der Vorsatzsand in Form einer Paste auf den gesamten Formhohlraum und die Angusskanäle aufgetragen, was dem fertigen Gussstück eine gute Oberflächenbeschaffenheit verleiht.
Mithilfe eines Kernkastens wird ein trockener Sandkern vorbereitet. Nach dem richtigen Backen wird es wie auf dem Foto gezeigt in den Formhohlraum gelegt. Der Oberkasten wird wieder auf die Bremse gesetzt, wobei die Ausrichtung der beiden mittels der sichergestellt wirdStifte. Auf dem Oberkasten wird ein geeignetes Gewicht gehalten, um die nach oben gerichtete metallostatische Kraft während des Gießens von geschmolzenem Metall auszugleichen. Die Form ist nun, wie auf dem Foto gezeigt, zum Ausgießen bereit.
Zeitpunkt der Veröffentlichung: 25. Dezember 2020