Bei RMC Casting Foundry übernehmen wir dasHarzbeschichtete Sandform(kein Brenn- und Selbsthärtungsprozess) zum Gießen von Messing, Bronze und anderen Legierungen auf Kupferbasis.
Messinggussteilewerden aufgrund der hervorragenden Leistung der Messingmaterialien häufig im Ventil- und Pumpenbereich eingesetzt. Bei RMC Foundry produzieren wir hauptsächlichMessinggussteiledurch Grünsandguss, harzbeschichteten Sandguss,Feingussund für große Messinggussteile wenden wir auch das Schaumguss- und Vakuumgussverfahren an. Im Allgemeinen sind die im Sandgussverfahren hergestellten Messinggussteile die Hauptkategorie in unserer Gießerei.
Eine Kupferlegierung mit Zink als Hauptlegierungselement wird üblicherweise als Messing bezeichnet. Eine binäre Kupfer-Zink-Legierung wird als gewöhnliches Messing bezeichnet, und ternäres, quartäres oder mehrelementiges Messing, das durch Zugabe einer kleinen Menge anderer Elemente auf der Basis einer Kupfer-Zink-Legierung gebildet wird, wird als Spezialmessing bezeichnet. Messingguss wird zur Herstellung von Messing für Gussteile verwendet. Messinggussteile werden häufig im Maschinenbau, bei Ventilen und Pumpen, auf Schiffen, in der Luftfahrt, im Automobilbau, im Baugewerbe und in anderen Industriebereichen eingesetzt. Sie nehmen bei schweren Nichteisenmetallmaterialien ein gewisses Gewicht ein und bilden Messinggussserien.
Im Vergleich zu Messing und Bronze ist die Feststofflöslichkeit von Zink in Kupfer sehr groß. Unter normalem Temperaturgleichgewicht können etwa 37 % des Zinks in Kupfer gelöst werden, und etwa 30 % des Zinks können im Gusszustand gelöst werden, während Zinnbronze im Gusszustand den Massenanteil der festen Löslichkeit von Zinn ausmacht in Kupfer beträgt er nur 5 bis 6 %. Der Massenanteil der festen Löslichkeit von Aluminiumbronze in Kupfer beträgt nur 7 % bis 8 %. Daher hat Zink in Kupfer eine gute Lösungsverfestigungswirkung. Gleichzeitig können die meisten Legierungselemente in unterschiedlichem Maße auch in Messing gelöst werden, was seine mechanischen Eigenschaften weiter verbessert, sodass Messing, insbesondere einige Spezialmessinge, die Eigenschaften einer hohen Festigkeit aufweisen. Der Preis von Zink ist niedriger als der von Aluminium, Kupfer und Zinn und es ist reich an Ressourcen. Messing wird relativ viel Zink zugesetzt, sodass die Kosten für Messing niedriger sind als für Zinnbronze und Aluminiumbronze. Messing hat einen kleinen Erstarrungstemperaturbereich, eine gute Fließfähigkeit und ein bequemes Schmelzen.
Da Messing die oben genannten Eigenschaften hoher Festigkeit, niedrigem Preis und guter Gussleistung aufweist, gibt es für Messing mehr Sorten, eine größere Produktion und eine breitere Anwendung als Zinnbronze und Aluminiumbronze in Kupferlegierungen. Allerdings sind die Verschleißfestigkeit und die Korrosionsbeständigkeit von Messing nicht so gut wie die von Bronze, insbesondere sind die Korrosionsbeständigkeit und die Verschleißfestigkeit von gewöhnlichem Messing relativ gering. Erst wenn einige Legierungselemente hinzugefügt werden, um verschiedene Spezialmessinge zu bilden, wurde seine Verschleißfestigkeit und Korrosionsbeständigkeit verbessert und verbessert.
Als eine Art selbsthärtender Sand wird der No-Bake-Furanharzsand häufig für Grauguss-Sandguss- und Sphärogussverfahren verwendet. Die Oberfläche der Sandform würde nach dem Brennen der Beschichtung hart werden. Daher könnte das Furanharz-Sandgussverfahren zur Herstellung mittelgroßer und großer Eisengussteile von mehreren zehn Kilogramm bis hin zu mehreren zehn Tonnen eingesetzt werden. Mit guter Oberflächenqualität, engeren Maßtoleranzen und weniger Gussfehlern könnten die Furanharz-Sandgussverfahren zur Herstellung der komplexen Gussteile eingesetzt werden.
RMC nutzt das No-Bake-Sandgussverfahren zur Herstellung von Stahlgussteilen, Edelstahlgussteilen, Sphärogussteilen und Graugussteilen. Beim No-Bake-Verfahren werden Sandformen durch ein Holz- oder Metallmuster geformt. Der feinkörnige Sand wird mit einem Harzbindemittel in einem Hochgeschwindigkeits-Sandmischer vermischt und dann in einen Kasten mit dem Muster geworfen. Wenige Minuten später härtet das Sand-Bindemittel-Gemisch aus und die Form wird von den Modellen entfernt. Mit dem gleichen Verfahren werden gleichzeitig Sandkerne für die Innenstruktur der Gussteile hergestellt. Nachdem die Kerne und die Außenformen zusammengebaut sind, werden sie geschlossen und für das Metallgießen vorbereitet. Bestimmte Materialien, wie z. B. Gussteile aus duktilem Eisen, erfordern vor dem Gießen eine spezielle Behandlung des Metalls. Das No-Bake-Gießverfahren ist äußerst flexibel, da es die Einhaltung präziser Toleranzen bei Eisen- und Stahlgussteilen ermöglicht und gleichzeitig Teilegrößen von mehreren zehn Gramm bis hin zu mehreren zehn Tonnen verarbeiten kann.
Die Schritte des No-Bake-Shell-Casting-Prozesses:
No Bake ist ein Gießverfahren, bei dem zur Bindung des Formsandes chemische Bindemittel zum Einsatz kommen. Als Vorbereitung für das Füllen der Form wird Sand zur Formfüllstation transportiert. Mithilfe eines Mischers wird der Sand mit dem chemischen Bindemittel und dem Katalysator vermischt. Sobald der Sand den Mischer verlässt, beginnt der chemische Aushärtungsprozess des Bindemittels. Diese Formfüllmethode kann für jede Formhälfte angewendet werden (Oberkasten und Unterkasten). Anschließend wird jede Formhälfte verdichtet, um eine starke und dichte Form zu bilden. Anschließend wird die Formhälfte durch einen Rollover aus dem Modellkasten entfernt. Nachdem der Sand ausgehärtet ist, kann eine Formwäsche aufgetragen werden. Bei Bedarf werden Kerne in den Widerstand eingesetzt und der Oberkasten über den Kernen geschlossen, um die Form fertigzustellen. Eine Reihe von Formentransportwagen und Förderbändern bewegen die Form zum Gießen in die richtige Position. Nach dem Gießen lässt man die Form abkühlen, bevor man sie ausschüttelt. Beim Ausschüttelvorgang wird der geformte Sand vom Gussstück gelöst. Anschließend geht der Guss zu einem Gussendbearbeitungsbereich für die Entfernung des Steigrohrs, die Endbearbeitung des Gussteils und die Finalisierung. Die gebrochenen Formsandstücke werden weiter zerkleinert, bis der Sand wieder die Korngröße erreicht hat. Der Sand kann nun entweder zur Wiederverwendung im Gussprozess zurückgewonnen oder zur Entsorgung entfernt werden. Die thermische Rückgewinnung ist die effizienteste und vollständigste Methode zur Sandrückgewinnung ohne Backen.
Materialien für den Schalenformguss bei RMC Foundry | |
Metalle und Legierungen | Beliebte Note |
Grauguss | GG10~GG40; GJL-100 ~ GJL-350; |
Duktiles (Nodualar) Gusseisen | GGG40 ~ GGG80; GJS-400-18, GJS-40-15, GJS-450-10, GJS-500-7, GJS-600-3, GJS-700-2, GJS-800-2 |
Austemperiertes duktiles Eisen (ADI) | EN-GJS-800-8, EN-GJS-1000-5, EN-GJS-1200-2 |
Kohlenstoffstahl | C20, C25, C30, C45 |
Legierter Stahl | 20Mn, 45Mn, ZG20Cr, 40Cr, 20Mn5, 16CrMo4, 42CrMo, 40CrV, 20CrNiMo, GCr15, 9Mn2V |
Edelstahl | Ferritischer Edelstahl, martensitischer Edelstahl, austenitischer Edelstahl, ausscheidungshärtender Edelstahl, Duplex-Edelstahl |
Aluminiumlegierungen | ASTM A356, ASTM A413, ASTM A360 |
Legierungen auf Messing-/Kupferbasis | C21000, C23000, C27000, C34500, C37710, C86500, C87600, C87400, C87800, C52100, C51100 |
Standard: ASTM, SAE, AISI, GOST, DIN, EN, ISO und GB |
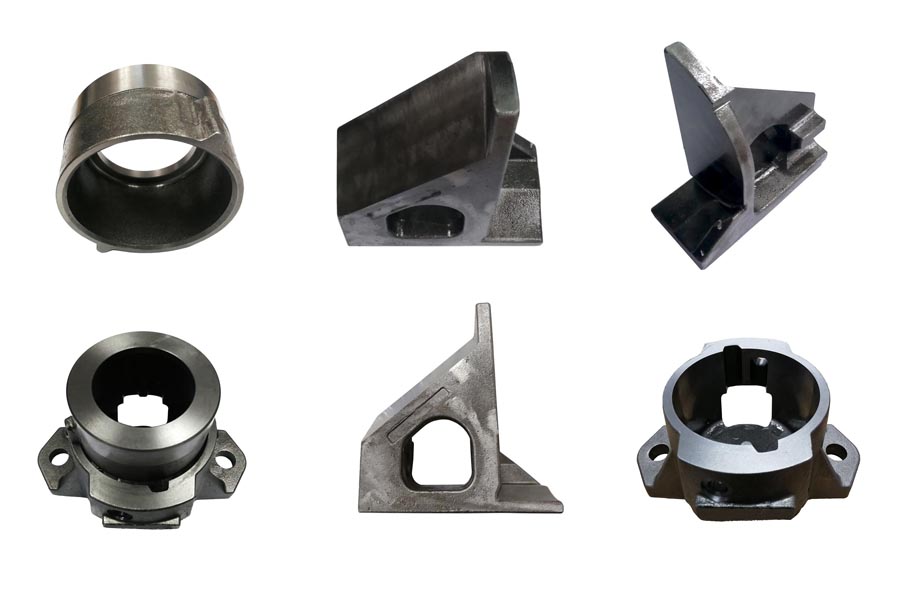
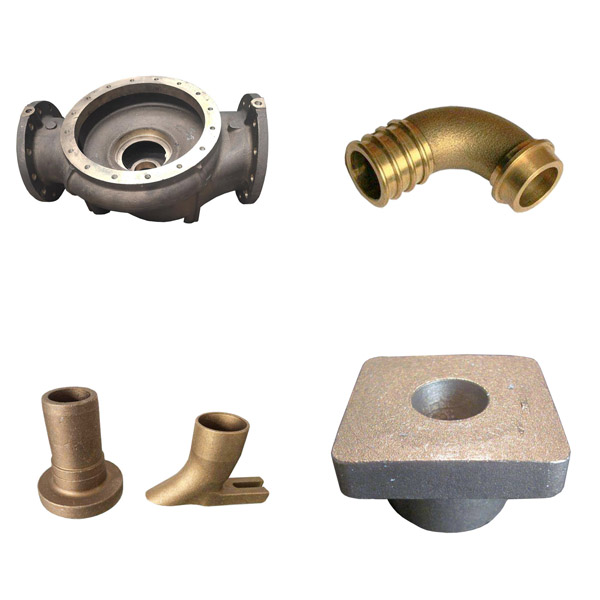